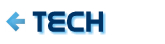
Your Cooling System
This illustrates a typical big block 396/402/427/454 cooling system. All small block systems are essentially the same with the exception of the bypass hose in most cases. Interesting to note the direction of the coolant flow; into the engine via the lower radiator hose and out of the engine via the upper hose. This is why a thermostat is invaluable.
Radiator Core
Radiators have ONE core but can have 2, 3, or even 4 rows of tubing. Many today use terms like 3 core and 4 core radiators when they really mean 3 or 4 rows.
A true 3 or 4 core radiator might have fitment issues.
Heater Core
One 'trick' some people like to do is removing the heater to save weight and running a hose from the outlet fitting on the intake manifold to the inlet fitting on the water pump. While this may save a few pounds of weight it reduces the cooling system capacity and leaves you without a heater as well as a defroster; something to think about in a tradeoff. Typically water does not circulate through the heater core unless the heater is turned on. Having this extra capacity can also help cool an engine on hot days by the very nature of more coolant and (if you can stand the heat), you can turn your heater on to circulate more coolant throughout your system and take advantage of the system's coolant capacity.
Thermostat
A thermostat allows the engine to circulate its coolant internally until the designated temperature of the thermostat is reached and allows coolant to flow into the top of the radiator. A thermostat is not designed to cool and engine but rather to allow the engine to come up to operating temperature. Thermostats come in various degrees of operation; 160°, 180° and 192°/195°. This is the temperature the thermostat begins to open.
A small cylinder is located vertically in the center of the thermostat and is filled with a wax that begins to melt at the designated temperature of the thermostat. A plunger connected to a valve presses into this wax as it melts pushing the plunger into the wax and opening the valve to allow water to circulate. When the engine is shut off, or at least cools down below the operating point of the thermostat, the wax begins to solidify and pushes the plunger back up via the spring and closes the valve.
Some people like to drill a couple of 1/8" holes in the valve to allow coolant to circulate into the radiator before the coolant has had a chance to get warm enough to open the thermostat. While this does work in a warm climate where it does not take the engine long to produce enough heat to open the thermostat, it might not be such a good idea when weather is cooler. It' will take longer for the engine to warm up thereby taking longer for the thermostat to open and give you heat through your heater or warm enough air to use your defroster.
There is a mistaken belief by some people that if they remove the thermostat, they will be able to solve their overheating problems. This could no be further from the truth. Removing the thermostat will allow uncontrolled circulation of the coolant throughout the system. It is possible for the coolant to move so fast that it will not be properly cooled as it races through the radiator, so the engine can run even hotter than before under certain conditions. Other times, the engine will never reach its operating temperature. On computer controlled vehicles, the computer monitors engine temperatures and regulates fuel usage based on that temperature. If the engine never reaches operating temperatures, fuel economy and performance will suffer considerably.
Keep in mind that thermostats have absolutely NO effect on your systems ability to cool, simply a regulator of the range it operates in. So, if you think a 160 will cure an engine running at 220 with a 180 thermostat, forget about it!
The graph above illustrates the importance of critical optimum coolant temperature is to the longevity and performance your engine. Cooler water makes horsepower and warmer water minimizes engine cylinder and bearing wear, or so it is commonly thought, but only to their own limits and ranges. There is a range where both optimum performance as well as minimal wear share similar characteristics. That number lies in the 175-180 degree range as shown by the overlap in the chart which correspondingly requires a 180 degree thermostat. FWIW, higher operating temperatures of today's engines are to fight combustion by-products and pollution. Also, engine oils are designed to work over a specific temperature range with optimum performance starting at temperatures that require the coolant to be the very same 175ish range.
Do not forget the moisture issue. Have you ever seen water vapor coming from your tailpipes? The very same thing happens INSIDE your engine. Your engine forms moisture inside when it cools and condensates. This moisture there is washed down into the oil when started and then awaits vaporization by internal temperatures rising enough to bring the moisture to the appropriate corrected boiling point. If enough moisture is left behind it combines with combustion byproducts to form acids that become dissolved in the oil itself. The oil becomes more acidic as the age of the oil progresses and picks on certain parts eventually. Also moisture will corrode other surfaces. So it is important to get your engine to a satisfying operating temperature as soon as possible. Usually oil pooling temps are about 30 to 40 degrees higher than the coolant temps. This is a generalized statement and can vary with load and engine design but you can see why you want your oil over 212 degrees to boil out the moisture immediately!
Years of research show use of 160 degree thermostats is way too low to be considered for performance or engine longevity. As the chart above illustrates, engine wear increased by DOUBLE at 160, than at 185 degrees. The 160s were invented for and commonly used in older, open loop cooling systems where only 6 pound radiator caps were used, and low 212 degree boiling points were the limit. We know better now.
Many early hot rodders found the 160s to be a smidgen better performing than the 195s, however the 180 appears to satisfy both ends of the spectrum. The correct water temperature and thus resulting metal operating temperatures required for the cylinders to achieve a minimum specific temperature in order to allow a fully mixed Air/Fuel charge to combust efficiently is a minimum of 180 degrees coincidentally. If you use 160s be aware that this can have a degrading effect over a time on your engine. I know a lot of rodders still using them however to whatever ends they want...and that is okay. I just report what I learn and you decide what is best for you. I hope this satisfies you information junkies out there.
If you are running an electric fan (or fans), be sure to use some sort of sender or temp sensor to control what temperature the fans should come on and when they should go off. One can always use a manual switch but you may (1) forget to turn the fans on resulting in overheating, (2) turn the fans on immediately which will delay your engine's warm-up period or (2) forget to turn them off when you shut the engine off resulting in a dead battery. When you turn your engine off water temperature is going to rise before it begins to cool. Modern cars with electric fans use a temperature sensor to keep the fans running until the coolant temperature drops to a specific level before turning the fans off.
Boiling Point
At sea level, the boiling point of water is 212°F. As you rise from sea level, the boiling point will, as a rule, drop by 1°F for every 500 feet in increase of elevation. For example, at 5000 feet, water will begin to boil at 203°F, at 10,000 feet it boils at 194°F. Now, if water is under pressure, the boiling point will increase about 3°F for every 1 psi of pressure. My home town is reported to be 1,145 feet above sea level so water will boil here at about 208°-210°F. With a car running a 15lbs radiator cap it should raised the boiling point of water 45°F to about 243°F-255°F. Adding a coolant mixture to your cooling system will raise the boiling point even higher.
Boiling Point of Various Coolant/Water Mix Percentages at Rated Radiator Cap Pressures | |||||||
System Pressure | 0 PSI | 4 PSI | 8 PSI | 12 PSI | 16 PSI | 20 PSI | 24 PSI |
Plain Water | 212 | 225 | 233 | 242 | 252 | 260 | 265 |
33% Cooling Mix | 220 | 230 | 240 | 253 | 260 | 268 | 273 |
44% Coolant Mix | 224 | 234 | 245 | 257 | 265 | 272 | 279 |
50% Coolant Mix | 226 | 236 | 248 | 258 | 267 | 275 | 280 |
60% Coolant Mix | 231 | 241 | 253 | 264 | 273 | 280 | 285 |
The above figures assume sea level; adjust accordingly for your location's altitude.
Unless you are running an electric fan system that will continue running until a certain water temperature is reached by moving cool air over the radiator fins, your water temperature will rise somewhat when you turn your engine off due to the lack of air flowing over the cooling fins in the radiator.
Bypass System
The water pump bypass hose is a feature that allows water to flow around the engine, without passing through the radiator, while the thermostat is shut. This prevents hot spots around the engine which could lead to damage. The bypass also prevents pump cavitation when the thermostat is closed and it allows water circulation inside the cooling passages preventing steam pocket formation before the thermostat opens. Eliminating this hose risks pump life as cavitation shakes the impeller, shaft and bearing.
Food for thought - GM engineers figured this out in the 50s. The bypass channel on a small block Chevrolet engine is incorporated into the water pump itself on the driver side and flows into/from the driver side of the engine block. The bypass system is used to circulate water throughout the engine until the thermostat opens.
Ever wonder why when you purchased a replacement water pump for your 283/302/307/327/350 Chevrolet engine the water pump-to-engine block gaskets had 4 holes? The bypass system is incorporated into the engine block and water pump.
The 327 high performance engine, RPO L79, also incorporated
a hose from the top of the water pump to the intake manifold
as a second bypass.
Chevrolet's Mark IV big block 396/402/427/454 engine uses only the hose for its bypass system.
Early 1965 through 1968 Mark IV engine with a "short" water pump uses a bypass hose with a 90-degree bend due to the short distance between the water pump and the intake manifold.
The 1969 and later Mark IV engines have a "long"
water pump so the bypass hose is not as 'bent' as the
early engines. There are molded hoses with GM markings in the
aftermarket but many hobbyists will simply use a short length
of heater hose to accomplish the same task such as this 1969
L78 engine.
© ChevelleWorld